Alcast Company Fundamentals Explained
Our Alcast Company Ideas
Table of Contents9 Simple Techniques For Alcast CompanyThe smart Trick of Alcast Company That Nobody is Talking AboutNot known Incorrect Statements About Alcast Company Facts About Alcast Company Uncovered3 Easy Facts About Alcast Company DescribedThe Only Guide for Alcast Company
Chemical Contrast of Cast Aluminum Alloys Silicon promotes castability by decreasing the alloy's melting temperature level and boosting fluidity during spreading. Furthermore, silicon adds to the alloy's stamina and put on resistance, making it useful in applications where resilience is crucial, such as automobile components and engine parts.It also boosts the machinability of the alloy, making it easier to process right into completed products. In this method, iron contributes to the general workability of light weight aluminum alloys. Copper enhances electric conductivity, making it advantageous in electric applications. It likewise improves deterioration resistance and includes in the alloy's overall strength.
Manganese contributes to the stamina of aluminum alloys and improves workability. Magnesium is a light-weight element that provides toughness and influence resistance to aluminum alloys.
Alcast Company - The Facts
It enables the production of light-weight parts with exceptional mechanical properties. Zinc enhances the castability of aluminum alloys and helps regulate the solidification process throughout casting. It boosts the alloy's stamina and solidity. It is typically found in applications where intricate shapes and fine information are essential, such as ornamental spreadings and particular auto components.
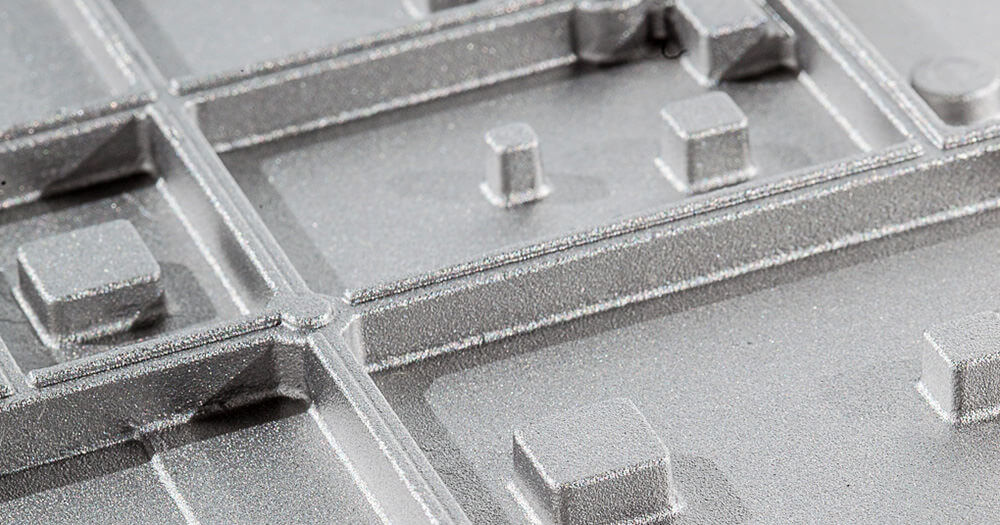
The main thermal conductivity, tensile toughness, return strength, and prolongation differ. Among the above alloys, A356 has the highest thermal conductivity, and A380 and ADC12 have the cheapest.
What Does Alcast Company Mean?
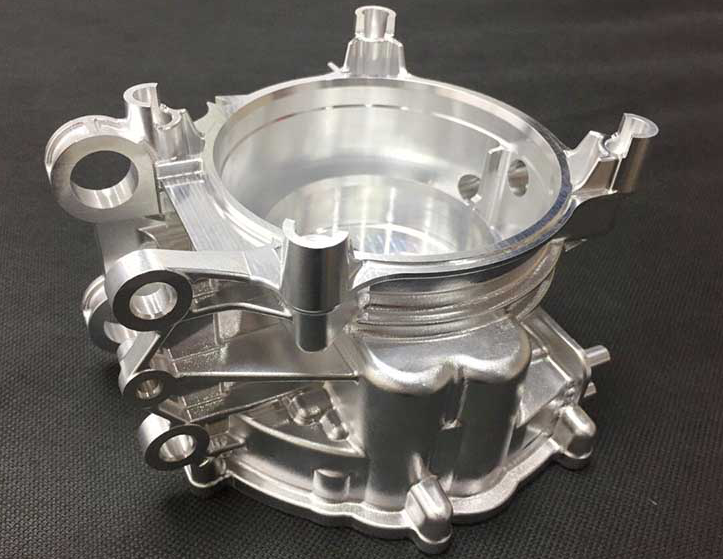
The A360 displays superior elongation, making it suitable for facility and thin-walled components. In accuracy casting applications, A360 is fit for sectors such as Customer Electronic Devices, Telecommunication, and Power Tools.
Our Alcast Company Statements
Its unique properties make A360 an important selection for precision spreading in these markets, enhancing product durability and top quality. aluminum casting company. Light weight aluminum alloy 380, or A380, is a widely made use of casting alloy with several distinct attributes.
In accuracy casting, light weight aluminum 413 beams in the Customer Electronics and Power Devices markets. It's commonly used to craft elaborate components like smart device housings, electronic camera bodies, and power tool coverings. Its accuracy is exceptional, with limited resistances approximately 0.01 mm, making sure flawless item assembly. This alloy's premium corrosion resistance makes it an exceptional selection for exterior applications, guaranteeing long-lasting, sturdy items in the pointed out industries.
The 25-Second Trick For Alcast Company
As soon as you have determined that the aluminum die casting procedure is suitable for your project, an important following action is deciding on the most ideal alloy. The light weight aluminum alloy you select will substantially impact both the casting process and the properties of the last product. As a result of this, you have to make your decision thoroughly and take an educated strategy.
Determining the most suitable aluminum alloy for your application will indicate weighing a wide selection of characteristics. The initial group addresses alloy attributes that influence the manufacturing process.
Some Ideas on Alcast Company You Should Know
The alloy you pick for die spreading straight influences several aspects of the spreading process, like how very easy the alloy is to deal with and if it is susceptible to casting problems. Hot breaking, additionally recognized as solidification cracking, is a regular die spreading flaw for light weight aluminum alloys that can result in interior or surface-level tears or splits.
Certain light weight aluminum alloys are a lot more prone to warm breaking than others, and your choice should consider this. Another usual defect discovered in the die spreading of aluminum is die soldering, which is when the cast sticks to the die walls and makes ejection difficult. It can harm both the cast and the die, so you ought to seek alloys with high anti-soldering homes.
Rust resistance, which is already a significant characteristic of aluminum, can differ significantly from alloy to alloy and is a necessary particular to think about depending upon the environmental problems your product will certainly be exposed to (aluminum casting manufacturer). Wear resistance is another property generally looked for in light weight aluminum items and can distinguish some alloys